Process takes textile recycling to new level
Research news
Researchers at Deakin University have found a way to separate blends of cotton-polyester material, providing a major breakthrough for recycling textile and other waste.
Each year, masses of material from unwanted clothing and other sources are deposited in landfill. The United States generates more than 11 billion kilograms of textile waste each year with only 15 per cent recycled and an estimated more than nine billion kilograms being sent to landfill, according to the US Council for Textile Recycling. The US EPA estimates that textile waste occupies five per cent of landfill mass. In Australia, the Technical Textiles & Nonwoven Association estimates that a massive one trillion tons of fibrous waste, generated from the textile, clothing and footwear processing industries is buried in landfills each year.
A significant hurdle to recycling waste clothing and other textiles back into their original fibres is that most of this material is composed of blended fibres – the most common being polyester/cotton blends. While it is easy to recycle cotton and polyester individually, it is not possible to mechanically separate the blends, where the fibres are closely bonded together. Chemical solutions attempted to date have not been viable economically or environmentally.
Now, using an ionic liquid (a salt in a liquid state) researchers at Deakin’s Institute for Frontier Materials, Dr Nolene Byrne and PhD student Rasike De Silva have developed a simple process to separate polyester-cotton blends into their individual components.
Unlike harsh solvents which have previously been used to dissolve polyester, ionic liquids provide an environmentally friendly solvent to chemically separate polyester/cotton blends. Another benefit of using ionic liquids, says Mr De Silva, is the ease with which the polyester and cotton can be separated.
“The ionic liquid selectively dissolves the cotton component, with the added advantage that the liquid can then be recycled and reused. This cotton can then be regenerated into various forms, such as spun into fibres or cast as cellulose films, like cellophane,” he explains. The recovered polyester can also be recycled by melting and reshaping it into other forms, such as plastic bottles or fibres.
Regenerated cellulose fibres such as viscose, rayon and lyocell have a considerable market share and are growing in popularity. Regenerated cotton is also increasingly being used as a low-cost precursor in the carbon fibre industry and as the starting material for bioethanol production.
The researchers say the new process is not limited to textile recycling but can also be applied to recycling any type of biocomposite material, including those used in the automotive industry.
Mr De Silva, a textile engineer from Sri Lanka, is working at the Institute for Frontier Materials with Dr Nolene Byrne and Professor Xungai Wang. He carried out the project as part of his PhD research into separation and utilisation of polymer fibre blends using environmentally friendly approaches.
The process described here has recently been published in the journal RSC Advances: http://pubs.rsc.org/en/content/articlelanding/2014/ra/c4ra04306e#!divAbstract.
Share this story
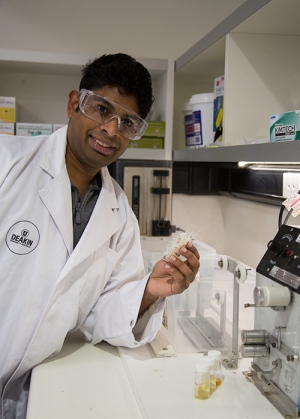