Concrete outcome for carpets
Research news
Thousands of tonnes of textiles waste that would normally go to landfill annually in Australia could soon be given new life within cement footpaths, driveways and roads.
In an Australian-first, a collaboration between Deakin scientists and Geelong's GT Recycling and Godfrey Hirst has resulted in the development of technology that can recycle polymer textiles.
“Given Geelong’s long history in textiles, it is fitting that this innovative solution to textiles recycling has been developed here – and local businesses should be the first to benefit,” said Professor Peter Hodgson, Director of Deakin’s Institute for Frontier Materials.
GT Recycling - established in Geelong in 1998 and run by two generations of the McLean family - collects, sorts and processes plastic and cardboard waste from landfill sites and manufacturers across Victoria. The recycled plastic is given new life by local and overseas manufacturers.
“There has been no carpet recycling technology on the market in Australia, but we knew there was potential, as the majority of textile wastes are polymeric materials, particularly in carpet, that could be recycled in a similar way to other plastics,” explained Trevor McLean, General Manager at GT Recycling.
“We are also optimistic that the new process will potentially create new employment opportunities in the region in the future.”
Achieving this breakthrough has been Trevor McLean’s pet project for the past 10 years. “The Federal Government’s “Enterprise Connect” program provided the way forward,” he explained.
“The grant supported a Deakin recycling expert, Dr Mary She, to work closely with us over the past two years.”
Dr She brought her own ten years of textiles recycling expertise to the project, along with the support of a wider team of researchers, led by Professor Lingxue Kong, from Deakin’s Institute for Frontier Materials.
“This project aligned perfectly with Deakin’s commitment to serve our local community,” said Dr She. “It also reflects our wider focus on fibre – exemplified by Carbon Nexus – and it is fantastic for the environment that we can help to reduce textiles waste in this way.”
Mr Kim McKendrick, the CEO of Godfrey Hirst – the other key player in the project - added that disposing of textiles waste has been a challenge to the textiles industry.
“We have a strong commitment to sustainable manufacturing and disposal, and have supply chain control of our operations, from fibre making to delivery. Recycling our offcuts and used carpets will be the final link in the chain,” said Mr McKendrick.
“Working with Dr She and GT Recycling, we have been able to modify the polymers in our carpets to optimise recycling potential, without affecting the quality of the carpet.”
Godfrey Hirst was one of Australia’s first textile mills - established in 1865 – and is now Australasia’s largest carpet manufacturer. Its head office and manufacturing facility are still in Geelong - located on a 33-hectare site in South Geelong.
So how will the recycled carpet be used?
Deakin’s Professor Lingxue Kong explained that the recycled textile fibres – to be known as “GTfibrecrete” - will be perfect for use as reinforcing in footpaths, gravel and road surfaces.
“By adding less than four per cent of polymer fibres to cement paths, we have seen less cracks, less rain damage, greater flexibility and improved durability – and we have removed the need for wire mesh in certain applications. This will result in longer life and less maintenance, which should be very attractive to councils across Australia,” Professor Kong said.
“The recycled fibres will cost only a fraction of the new fibres, which cost up to $30 a kilo, and they are virtually indistinguishable from the new fibres from a performance perspective.”
Professor Kong is optimistic that, in the medium-term, the recycled fibres will be adopted by the broader construction industry - and our old carpets will find new life in our walls and ceilings - as well as underfoot.
Share this story
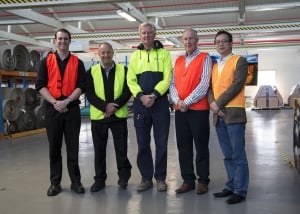